project09:2024Msc2JIP: Difference between revisions
JIPStudent (talk | contribs) |
JIPStudent (talk | contribs) |
||
Line 36: | Line 36: | ||
Lunar regolith, the loose soil covering the Moon's surface, is rich in minerals such as silica, magnesium oxide, and calcium oxide, which can be processed into a form suitable for 3D printing. Its abundance and mineral composition make it ideal for creating building blocks, as it reduces the need for external materials. However, regolith presents unique challenges due to its abrasiveness, reactivity, and the extreme lunar environment, which requires specific adaptations in the 3D printing process. | Lunar regolith, the loose soil covering the Moon's surface, is rich in minerals such as silica, magnesium oxide, and calcium oxide, which can be processed into a form suitable for 3D printing. Its abundance and mineral composition make it ideal for creating building blocks, as it reduces the need for external materials. However, regolith presents unique challenges due to its abrasiveness, reactivity, and the extreme lunar environment, which requires specific adaptations in the 3D printing process. | ||
'''Selective Laser Sintering''' | |||
Selective Laser Sintering (SLS) is a key 3D printing technique utilized in the Lunar Constructors project for creating durable building blocks from lunar regolith. SLS operates by using a high-powered laser to selectively heat and fuse particles of regolith layer by layer, forming a solid structure without requiring any additional binding materials. This method is particularly advantageous for lunar applications, as it produces strong, precise blocks entirely from local resources, aligning well with the project’s goal of in-situ resource utilization (ISRU). | |||
SLS stands out as a robust method for producing high-quality, regolith-based building blocks on the Moon. Its precision, durability, and ability to use 100% local material make it ideal for constructing stable, autonomous structures suited to the Moon’s extreme conditions. By incorporating SLS into the Lunar Constructors project, the team can ensure that lunar habitats are both sustainable and resilient, supporting future missions with reliable, locally manufactured infrastructure. | |||
'''JSC-1 Lunar Simulant''' | |||
The JSC-1 lunar soil simulant, created by NASA’s Johnson Space Center, is primarily composed of basaltic volcanic ash. Its chemical makeup, mineralogical properties, and particle size distribution closely match those of lunar low-titanium mare soils, such as those gathered during the Apollo 14 mission. Specifically, JSC-1 contains oxides like silicon dioxide (SiO2), aluminum oxide (Al2O3), and calcium oxide (CaO), which are also abundant in lunar soil. In addition, JSC-1 contains minerals like plagioclase, pyroxene, and olivine, which are the main components of lunar basalts and soils. This allows it to simulate lunar soil conditions effectively for 3D printing studies. JSC-1’s physical characteristics, such as the angle of internal friction and cohesion, are similar to those of lunar soils, making it suitable for studying lunar surface construction | The JSC-1 lunar soil simulant, created by NASA’s Johnson Space Center, is primarily composed of basaltic volcanic ash. Its chemical makeup, mineralogical properties, and particle size distribution closely match those of lunar low-titanium mare soils, such as those gathered during the Apollo 14 mission. Specifically, JSC-1 contains oxides like silicon dioxide (SiO2), aluminum oxide (Al2O3), and calcium oxide (CaO), which are also abundant in lunar soil. In addition, JSC-1 contains minerals like plagioclase, pyroxene, and olivine, which are the main components of lunar basalts and soils. This allows it to simulate lunar soil conditions effectively for 3D printing studies. JSC-1’s physical characteristics, such as the angle of internal friction and cohesion, are similar to those of lunar soils, making it suitable for studying lunar surface construction |
Revision as of 16:02, 14 November 2024
MSc 2 JIP Space Architecture & Infrastructure
The Lunar Constructors project is aimed at addressing one of the most pressing challenges in space exploration: creating sustainable, autonomous habitats on the lunar surface. As space agencies and private companies advance their capabilities for lunar missions, the goal of establishing long-term human presence on the Moon is becoming more tangible. However, the Moon's environment presents extreme challenges—including intense radiation, a lack of atmosphere, severe temperature fluctuations, and the impact of micrometeorites—that make traditional human-centric construction methods risky and complex.
The project addresses these challenges by proposing an autonomous, modular system for constructing lunar habitats, utilizing local resources and advanced robotic and manufacturing technologies. The project's approach combines three key technological domains:
- Building Blocks: For building a very basic structure on the Moon, the Lunar Constructors use a very basic part of a structure, the building blocks. For a structure to be established by a swarm of robots, the building blocks required to be assembled should be simple structures to decrease the complexity of assembling the structure by the robot. Another aspect to be considered is the complexity involved with 3D printing, hence choosing a building block which is simple yet strong is very important.
- 3D Printing: Additive manufacturing methods, specifically adapted for lunar conditions, are used to transform regolith into interlocking building blocks. Techniques such as binder jetting and selective laser sintering allow the creation of complex structures that are lightweight yet resilient, accommodating the Moon's low gravity and atmospheric conditions.
- Swarm Robotics: Employing a decentralized system of robots that work collaboratively, each robot is designed to perform specific tasks, such as regolith collection, transportation, and assembly. Inspired by swarm intelligence, this autonomous approach allows a large number of small robots to adapt dynamically, perform tasks collectively, and compensate for any individual failures—critical attributes for construction in the harsh lunar environment.
The Lunar Constructors project tries to address the feasibility of lunar construction through a series of targeted objectives. This includes researching future robust 3D printing processes using lunar regolith simulants, designing efficient robot interactions for swarm-based construction, and simulating the assembly of various structures within the Gazebo simulation environment. The project also evaluates potential building designs, such as pyramidal and dome-shaped structures, which are suited to the lunar environment's unique demands.
By leveraging advanced autonomous systems and local materials, Lunar Constructors aims to contribute significantly to global efforts in space exploration. This project offers a scalable, sustainable approach to lunar habitat construction, helping to pave the way for future missions and long-term human presence on the Moon.
Problem Statement
The project aims to perform a feasibility study of setting up a structure on the surface of the Moon by using in-situ resources to 3D print the structure and assembling it using a swarm of robots.
Concept of Operations
A general concept of operations was developed to have a clear perspective of the mission. Figure 1 illustrates the concept of operations of the Lunar Constructors project. As illustrated in the figure, from the swarm of robots available, one of the robots collects lunar regolith, which is fed to a 3D printer to produce blocks for the structure. The blocks are then transported to a site by the robots, where they use their swarm intelligence to build a structure using a predefined rule set.
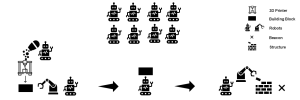
Building Blocks
For the project, interlocking blocks were chosen as the preferred building component for constructing autonomous, durable structures on the Moon. These blocks are designed to simplify the assembly process, providing a stable and adaptable modular unit that a swarm of autonomous robots can handle and stack effectively. The interlocking blocks offer unique advantages in both structural integrity and ease of manipulation, making them particularly suitable for the challenging conditions of the lunar environment.
The interlocking blocks are engineered with simple yet effective connectors that allow each block to securely interlock with adjacent units. This design enables a robust stacking system that holds up well under the Moon’s low-gravity conditions. An illustration of the interlocking building blocks are shown below.

3D Printing
The 3D printing component of the Lunar Constructors project is crucial for producing building materials on the Moon, using locally sourced lunar regolith to create modular blocks for habitat construction. By employing in-situ resource utilization (ISRU) and advanced 3D printing methods, the project aims to transform lunar regolith into durable, interlocking blocks that are suitable for autonomous assembly. This approach minimizes the need for Earth-based materials, reducing transportation costs and logistical complexity, while providing a sustainable method for constructing lunar infrastructure.
Lunar regolith, the loose soil covering the Moon's surface, is rich in minerals such as silica, magnesium oxide, and calcium oxide, which can be processed into a form suitable for 3D printing. Its abundance and mineral composition make it ideal for creating building blocks, as it reduces the need for external materials. However, regolith presents unique challenges due to its abrasiveness, reactivity, and the extreme lunar environment, which requires specific adaptations in the 3D printing process.
Selective Laser Sintering
Selective Laser Sintering (SLS) is a key 3D printing technique utilized in the Lunar Constructors project for creating durable building blocks from lunar regolith. SLS operates by using a high-powered laser to selectively heat and fuse particles of regolith layer by layer, forming a solid structure without requiring any additional binding materials. This method is particularly advantageous for lunar applications, as it produces strong, precise blocks entirely from local resources, aligning well with the project’s goal of in-situ resource utilization (ISRU).
SLS stands out as a robust method for producing high-quality, regolith-based building blocks on the Moon. Its precision, durability, and ability to use 100% local material make it ideal for constructing stable, autonomous structures suited to the Moon’s extreme conditions. By incorporating SLS into the Lunar Constructors project, the team can ensure that lunar habitats are both sustainable and resilient, supporting future missions with reliable, locally manufactured infrastructure.
JSC-1 Lunar Simulant
The JSC-1 lunar soil simulant, created by NASA’s Johnson Space Center, is primarily composed of basaltic volcanic ash. Its chemical makeup, mineralogical properties, and particle size distribution closely match those of lunar low-titanium mare soils, such as those gathered during the Apollo 14 mission. Specifically, JSC-1 contains oxides like silicon dioxide (SiO2), aluminum oxide (Al2O3), and calcium oxide (CaO), which are also abundant in lunar soil. In addition, JSC-1 contains minerals like plagioclase, pyroxene, and olivine, which are the main components of lunar basalts and soils. This allows it to simulate lunar soil conditions effectively for 3D printing studies. JSC-1’s physical characteristics, such as the angle of internal friction and cohesion, are similar to those of lunar soils, making it suitable for studying lunar surface construction
Swarm Robotics
FINAL REVIEW